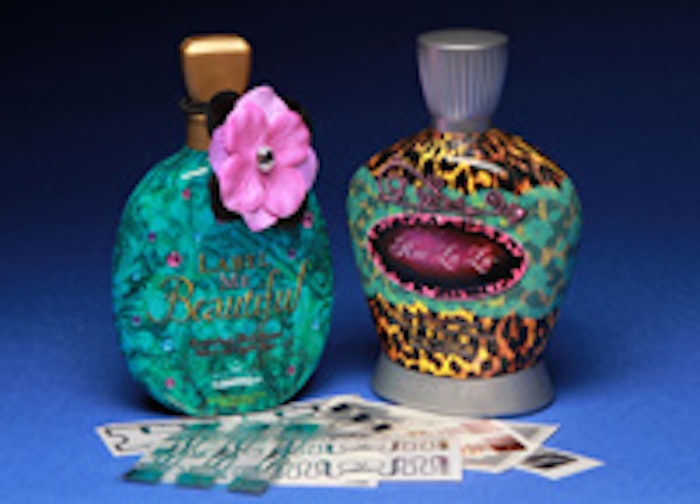
Professional salon products—shampoos, conditioners, styling aids and indoor tanning lotions—are increasingly showing up in unauthorized outlets such as online retail websites, drugstores, grocery stores, flea markets and so on. And this type of product diversion, although not illegal, hurts the beauty industry. Not only are beauty brand owners, distributors and salons being affected, but also consumers due to the fact that they are being sold products that are outdated, damaged, tampered with or counterfeit.
Diversion has had a detrimental effect on many businesses across the US, and it has been an industry-wide problem for professional tanning and beauty salons for years. According to New Sunshine, LLC, “Product diversion is the sale of products through an unauthorized, unofficial or unintended channel that damages brand integrity, erodes distributor loyalty, reduces salon profitability, and puts end-user customers at risk.”
Putting a Stop to Diversion
New Sunshine, a beauty company based in Indianapolis, has been fighting product diversion for more than 10 years. The company manufactures tanning lotions, such as Designer Skin, Australian Gold, Swedish Beauty and California Tan. With a product philosophy and positioning built on “nutrition of the skin” for its Designer Skin line, New Sunshine promises to provide the ultimate in skin nutrition through the use of advanced skin care ingredients and formulas.
However, the growing problem of product diversion has heightened the company’s need to protect its product philosophy and positioning to ensure its customers only receive its highest quality and safest products. To combat the problem, New Sunshine set out in December 2010 to find a way to “diversion proof” its collection of Designer Skin professional indoor tanning products, including its bronzers, lotions and tan extenders.
Diversion is disruptive to salon owners because it reduces sales when third parties undercut the price of salon products and, in turn, reap huge profits. With 15,000 salon partners and 19 distributors, New Sunshine was looking to make an investment in not only protecting the goodwill of its brand, but also in protecting its salon partners and distributors, as well as consumers. New Sunshine does not sell its Designer Skin products directly; therefore, it counts on its distributors to only sell its lotions to professional salons.
“In the past, our customer service department has reported situations in which our bottles have been filled with generic brands of lotion, then sold online as authentic products,” says Scott Matthews, general counsel, New Sunshine. “End users expressed concerns about us having changed or cheapened our formula.” The diversion problem prompted New Sunshine to look for a way to ensure full chain-of-custody protection for its products—from manufacturing to the customer. For help, it turned to WS Packaging Group and its radio-frequency identification (RFID) experts for an innovative solution that would enhance security throughout its entire supply chain and help put a stop to product diversion.
RFID uses radio frequency signals to power a passive RFID tag or label attached to a product to capture the tag's information. The data encoded to the tag or label helps identify and track that product, and this ability to track the product via RFID allows a business to identify product sold via unauthorized distribution channels, such as the Internet.
At shipment, each product’s unique RFID serial number is captured and associated to a particular customer sales order. Therefore, once a business receives the product it can read the serial number and know immediately who the product was sold to originally. And knowing this information, the brand owner can identify who is diverting its products. Without RFID, a business would have no real efficient way to capture serial numbers at shipment and quickly associate a product to a particular customer’s purchase order.
“Within two weeks of launching a new product, New Sunshine experiences diversion with the product being sold on the Internet,” says Michael Manley, RFID consultant with WS Packaging. “Diversion damages a brand’s identity and hurts consumer loyalty. New Sunshine felt it was important to re-establish customer confidence by taking a leadership position with RFID for product protection.”
Defining the Serialization Strategy
WS Packaging representatives met with the executive team at New Sunshine for initial discussions to address its diversion problem and possible solutions. The first step was defining the serialization strategy. Serialization, a requirement of RFID, enables a business to track its inventory by distinct serial numbers given to each individual product. Since RFID tags are serialized, several tags can be read at once, and the serial numbers are recorded and stored in a database.
“In order to define the serialization strategy, New Sunshine needed to make three key decisions—what will the data carrier be (bar code or RFID), how will the serial numbers be managed, and what will be the serialization encoding scheme,” Manley says. “Further, what are the implications to existing business processes with each data carrier.” After gaining a deeper understanding of New Sunshine’s manufacturing and order fulfillment process, it became clear that RFID would have the least impact to operations and packaging design, could scale up quickly, and would be the most efficient approach for downstream trading partners.
WS Packaging created a serialization-encoding scheme that consisted of a grandparent, parent and child RFID tag relationship. The tag on the pallet is known as the grandparent, the tag on the case as the parent, and the tag on the actual product as the child. Each tag consists of a data identifier—“P” (pallet), “C” (case) and “B” (bottle)—followed by a serial number, allowing the RFID reader to easily identify the product and associate it with a unique sales order and determine if the number was an item, case or pallet.
New Sunshine has two operations located in Tempe, Arizona—a manufacturing facility and a distribution center—and all product development, bottle production and labeling (RFID and prime) takes place in the manufacturing facility. The bottles are high-density polyethylene, and the prime labels are pressure sensitive or shrink wrap.
“For New Sunshine, it was essential that the RFID tagging system not have a significant impact on operations,” Manley notes. “The selection of the data carrier (RFID or bar code) significantly impacts the business processes, such as picking and order fulfillment. RFID can read an entire box full of bottles without incremental labor, whereas bar code increases labor by requiring a user to handle each individual bottle and scan the bar code due to the fact that it is an optical line-of-sight technology.”
The second step was prequalification—a systematic process for identifying all appropriate RFID subsystem components, including reading equipment and the associated RFID tag inlay. The process is used to identify two or more RFID tag inlays that either meet or exceed operating margin requirements—the minimum power required to activate a passive RFID inlay on a product at both the item- and case-levels, and the readability of each item—for all desired use RFID tag reading applications.
“New Sunshine shipped us several Designer Skin product samples to conduct testing on,” Manley says. “We set up RFID portals to test a number of different tags to see which tags worked best for the client’s products. Suntan lotions have physical properties that can make reading RFID tags difficult, so it was crucial we find a tag that was sensitive enough to work well with their products and containers. In addition, it was vital that the tag be able to withstand the heat tunnel in which the shrink wrap is applied to many of the Designer Skin high-density polyethylene bottles.”
The Designer Skin product line consists of 14 different bottle shapes in a variety of sizes, ranging from 3.6 oz to 20 oz, with the majority of its bottles being 13.5 oz. “Not only was it critical that the RFID tag work properly with the tanning lotions and that we identify one tag size that is going to work across the range of bottle shapes and sizes, but also that the tag not intrude on the design of the package or label,” Matthews explains. “We are able to hide the RFID tag underneath the pressure-sensitive label or shrink wrap without having to give up valuable packaging real estate or impacting our brand image. This was a very important factor to us.”
With the RFID tag hidden behind the label or shrink wrap—applied horizontally to the wide bottles and vertically to the narrow bottles—an individual would have to cut off the pressure-sensitive label or shrink sleeve in order to remove the tag, making the product most likely un-resellable. “There’s no way to circumvent the system that we created,” Manley says. “This ensures product chain of custody.”
RFID Verification and Encoding
WS Packaging standardized one UHF Gen2 RFID inlay comprised of an Impinj Monza chip, antenna and a clear film substrate that is applied to a pressure-sensitive paper label. The RFID tags are produced, pre-encoded and tested at the WS Packaging facility in Algoma, Wisconsin, where the company enforces a thorough quality inspection process that sees that each incoming roll of RFID inlays is checked for bad inlays. WS Packaging ensures there are no duplicate inlays and that each is unique. Each finished tag is serialized and a log file is created for each one. The tags are then provided to New Sunshine on a master roll. The roll of tags is put into a label dispenser and applied by hand to each Designer Skin bottle, underneath the prime label or shrink wrap. “This system is robust and secure,” Manley says. “New Sunshine can have 100% confidence in the tags that WS Packaging provides to them. Each tag across all bottles, cases and pallets is unique. And if a product was subject to diversion, New Sunshine will be able to easily identify the source.”
“After finding the right tag for the different products, we reviewed New Sunshine’s business processes and mapped out the process flow,” Manley adds. “Then we identified the objectives of the RFID pilot and acceptance criteria, focusing on two key elements: does the system function as designed and did we deliver what we promised. We also identified the required RFID hardware, software and resources. Once New Sunshine approved the system design, we developed the necessary software and worked in a collaborative manner with the IT department at New Sunshine to ensure the RFID readers and database were up and running properly. Operator training was also conducted and completed. The system is simple in its operation.”
New Sunshine is rolling out the RFID tagging process in 2012 and will continue to add to it to its products in the future. “Through RFID technology we hope to better detect who is selling our products through unauthorized channels,” Matthews says. “We recognize diversion as a problem in our industry, and we want to be a part of the solution.”