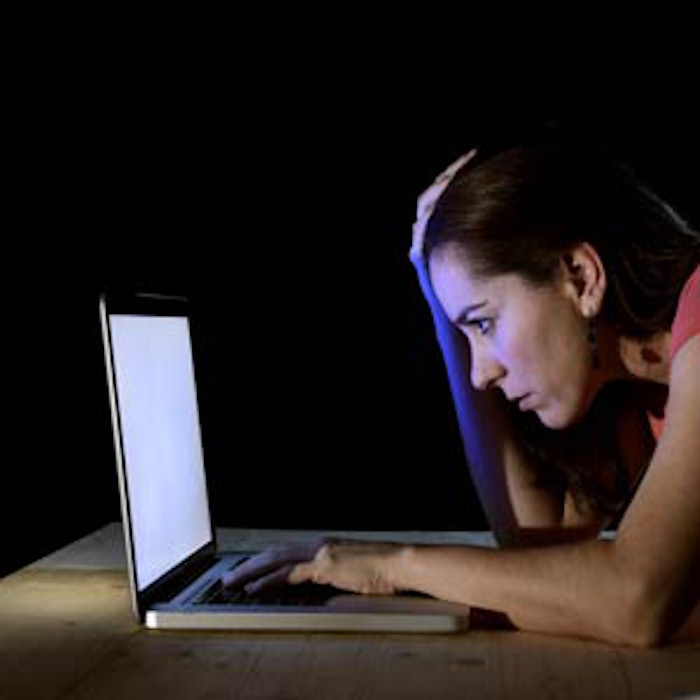
- Quality control is the part of your operation that is supposed to make all the moving parts function as they are supposed to.
- No one knows your standards for what the product is supposed to look like as you do. n You need to do the basic quality control yourself because sometimes things go wrong.
- Unless you have a way to find the problems, the problems will find you, and they’ll usually find you when it is a lot harder to deal with them.
- The sooner you find problems, the easier and cheaper they are to fix.
- In a problem situation, clearly thought out specifications will protect you and your brand.
Further reading: Top Questions to Ask Before Developing a Beauty Product
It all leads up to this—the launch of your new product. Tomorrow’s success depends on today going well. All the innovation, the planning, the development, the testing, the legal and regulatory reviews, the performance testing, the manufacturing start-up, the shipping—all of it comes together to roll your new product out into the marketplace. Even if day one goes well, things still need to go smoothly to build the brand.
Introducing a new product involves many moving parts that all have to work correctly. Quality control (QC) is the part of your operation that is supposed to make all these components function as they are supposed to.
Quality assurance (QA) is also an important part—the policies, procedures and agreements that give the plan for how things are supposed to work—but it’s not the whole picture. You must actually control the moving parts so that the QA policies, procedures and agreements all actually happen as designed.
No One Knows Your Product Better Than You
It’s tempting to rely on the vendors in your supply chain to provide control over the parts of the process that each of them has sold you. You chose each vendor carefully to provide the components for your product, satisfying yourself that they each do great work. But you still need to do the basic QC yourself. No one knows your standards for what the product is supposed to look like as you do. Your suppliers are there to sell you things, and although they may do their best to deliver the things they believe meet your standards, you won’t know whether they are good enough unless you look yourself. Production start-ups often, perhaps usually, produce things that are almost as good as they are supposed to be—right on the border. Unless you are looking at the quality of each of the components of your product, you take the risk that “almost good enough” things get into your product, making the overall quality less than it should be.
When Things Go Wrong
Sometimes things go wrong. Not almost wrong, but clearly wrong. Unless you have a way to find the problems, the problems will find you, and they’ll find you when it is a lot harder to deal with them. Your own QC efforts will allow you to stay a step ahead of problems on your own terms.
When a production problem does happen, you will probably find that your manufacturer will spend significant effort proving that the problem isn’t their fault or responsibility. Production will grind to a halt and your manufacturers and vendors will all blame each other for the problem, each protecting their own business first and foremost. Meanwhile, your shipping deadlines will have more to do with “dead” than “line.” Any solution to the problem that your vendors come up with may or may not produce your product in the best possible way.
If you have QC as part of your operation, you are in a much better position to determine yourself how the problem happened and who is to blame. These are the key elements in getting production running again. You can then work out the changes to the production process that protects the quality of your product best.
A benefit to aggressively controlling quality, especially during first production runs, is that the amount of unacceptable product generated is much smaller than if you find out about the problem when the production run is over. In the latter case, you are faced with reworking or replacing everything, instead of just a few pieces. With packaging components often coming from overseas, lead-times for replacement packaging can spell the end of a deal to sell your product.
A QC Checklist
Your QC program needs to check all of the key parts of your product. Make sure the bulk product matches the lab sample that you approved at the end of the development process. The differences between what the lab can make and what can be done in production are sometimes significant. Check the bulk carefully before anything gets filled so you won’t waste package components that probably take a long time to replace.
Similarly, check the package components before they are brought to the filling line. Delays in development and initial production plans all compress at the production start-up, so it usually feels like there is no time to inspect packaging components carefully to make sure they function and that they look like they are supposed to. Samples sent by the supplier ahead of the actual shipment may or may not represent what is on the pallets that are delivered to the filler. Taking the time to look at some statistical sampling of the shipment will give you a lot more confidence when production does actually start.
Making sure parts fit together correctly, especially if they come from different factories or suppliers, will head off production problems before they happen. Again, you need to look at some reasonable statistical sample of the parts, not just a few pieces. Stock packaging can have problems, but initial production of custom packaging components often has glitches. The sooner you find those problems, the easier and cheaper they are to fix.
The production process itself can have pitfalls even if all of the parts of the product look good. Did they get the product into the package correctly? Did they get the right amount in the package? Did they put the package together correctly? Does the surface of the hot-pour look like it is supposed to?
Being there for initial start-up will allow you to verify that the filler’s QC efforts are effective, that the fill weights are within specification, that the caps are on tight enough and that the folding cartons and liners are assembled correctly—the way you want them put together.
Setting QC Parameters
QC needs specifications, the parameters that describe what is acceptable and what is not for each part of your product. If it’s your product, they should be your specifications. Your suppliers are trying to keep you happy, but they are always protecting their own business at the same time. Leaving the specifications for your product to the vendors invites problems if things go sideways. “But they are within the specifications that you approved,” is what you might well hear in that kind of situation.
When submissions from the vendors come in, make sure the specifications for each submission sufficiently protect your interests. Common sense will help most of the time, but sometimes enlisting help from those who have technical experience is necessary to evaluate proposed specifications. In a problem situation, clearly thought out specifications will protect you and your brand.
Be Prepared
Murphy’s Law happens to everyone, eventually. It’s not the creative, fun part of the business, but having QC as a functioning part of your operation will keep you a step ahead of Murphy and protect your brand.
Cosmetics and personal care technical consulting expert Howard Baker is managing member of Product Integrity Laboratory LLC, which provides product development and quality control/quality assurance services for companies in the fragrance and cosmetic industry that use contract manufacturers. A cosmetic chemist with more than four decades of experience in the beauty industry, Baker has overseen product development and has provided technical consulting services in the areas of formulation development, product development testing, quality assurance and quality control, and regulatory compliance.