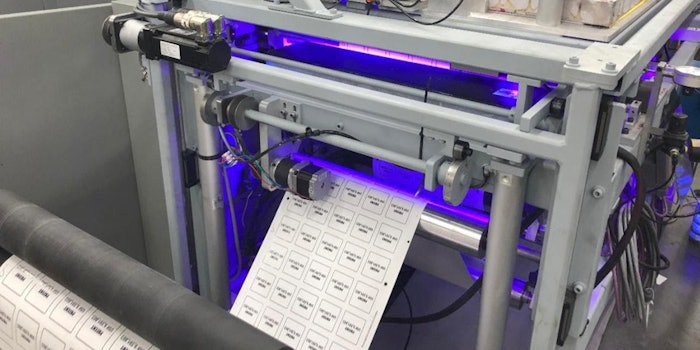
Empire Screen Printing has developed its UV LED ink curing technology over the last decade to keep employees safe and reduce pollution. Developed to replace UV curing via mercury bulbs, UV LED curing technology is now used across 80% of Empire’s business.
Related: AA Labels Launches Affordable Express Print Service
UV LED is 98% more energy efficient than traditional UV mercury curing.
The combination of UV and LED in the manufacturing process doesn’t produce ozone emissions or volatile organic compounds (VOCs), eliminating the need for ventilation systems to cope with irritants and pollutants.
The curing process uses light instead of heat, allowing the company to print on thinner substrates and eliminate material distortion.
Other benefits include a reduction in energy and HVAC demands as well as a reduction in costs to run the presses.
Empire’s UV LED press holds mechanical tolerances of 0.001” and can hold color-to-color registration between 0.005”-0.007”.
John Freismuth, president of Empire Screen Printing, said, “Now that we’ve developed this LED curing technology, we’ve learned that there is simply no downside to sustainable printing and production. The end product is of the same or greater quality, which, thanks to our ongoing process improvements, is exceptionally high."
Freismuth added, "The benefits to our manufacturing process and the cost savings are great side effects to achieving our primary goal of protecting employees. By taking steps to protect our employees, we have also managed to protect the environment and provide sustainably printed products to customers. The efficient processes we’ve developed means we can offer more environmentally-friendly products to our customers without any additional cost."