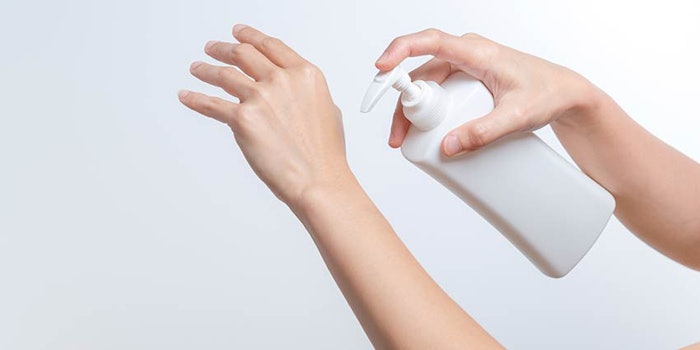
There are several different factors that influence the selection of both packaging and packaging machinery for liquid products, including the production rate, volume level and space requirements. But one of the most important elements is the liquid’s viscosity. The thickness of a liquid product will determine the ideal materials, as viscosity affects how liquid flows. Particularly in the cosmetics industry, viscosity among liquid products varies greatly.
Log in to view the full article
There are several different factors that influence the selection of both packaging and packaging machinery for liquid products, including the production rate, volume level and space requirements. But one of the most important elements is the liquid’s viscosity. The thickness of a liquid product will determine the ideal materials, as viscosity affects how liquid flows. Particularly in the cosmetics industry, viscosity among liquid products varies greatly.
Special report: Sustainability: On Top of Beauty's Packaging Agenda
Thin, less viscous liquids such as water will flow more freely, while highly viscous products that don’t flow as quickly or easily, such as gels and creams, will require more force when filling or dispensing product.
How Viscosity Shapes Packaging Choices
Often, viscous cosmetics such as creams and gels are filled into containers that are more user-friendly and help minimize waste. For some products like lotions, squeeze or spray bottles may be more appropriate, but many cosmetics are stored in jars that allow the user to remove the liquid by hand. The materials used for these viscous product containers can include plastic, acrylic, and glass.
Slippery Solutions
One liquid packaging development that has made the packaging of viscous liquids more efficient and user-friendly is slippery surface technology.
This new type of plastic will make the interior of bottles and other types of containers permanently wet using a layer of liquid. Containers lined with this substance can be used for a variety of products, including cosmetics and edible liquids such as ketchup. Using this technology, viscous liquid products packaged in squeeze bottles and other types of containers won’t get stuck like they have in the past.
While this innovation is still being developed, we’ll likely see it appear in liquid product packaging in the near future.
Packaging Equipment: Know Your Options
In addition to packaging, you also need to consider the type of equipment you’ll need to further maximize the efficiency of filling while reducing product waste in the packaging process. Certain types of packaging machines are designed to handle thinner products, while others are intended to fill thicker liquids using more forceful filling methods.
Lower Viscosities
- Overflow fillers: Overflow filling machines use nozzles that allow users to set specific fill levels for every container, regardless of any slight variation of volume. Once the liquid is filled to this level, the liquid will then overflow and go back into the supply to prevent product wastage. This filling method is often used for products such as water and other beverages but is also used for certain thinner cosmetics and personal care products.
- Gravity fillers: These fillers will fill liquids into containers using a time-based system, typically with a tang positioned above the fill heads to contain the supply of liquids. When the container is beneath the fill heads, a valve opens to let the supply fill the container to a fill level within a pre-set amount of time. Following this period, the valve closes to cut off the supply.
Viscous Cosmetics
- Pump fillers: These machines use single pumps for each fill head and can be time-based with an “on” and “off” feature. Controls for both pump rotation and speed are also available with many models and they are ideal for use with low- to high-viscosity liquids of all types.
- Piston fillers: Piston filling machines use a combination of a piston and cylinder to accurately fill containers. When the piston is removed from the cylinder, liquid is then transferred to it. The cylinder then fills to max capacity before the piston re-enters the cylinder to push the liquid into the containers. This machine is ideal for products with particulate or large chunks that the pump filler isn’t designed to handle.
Taking these types of packaging and machinery into consideration, you can determine which will be best for your liquid cosmetics products, thin or thick.
Michelle Pudlo joined E-Pak Machinery, Inc. in 2001 and is the marketing and trade show manager for E-Pak Machinery, Inc., Oden Machinery, Inc. and Change Parts, Inc. She is responsible for the marketing, communication and business development efforts of all three companies. In addition to strategic business development efforts, she directs media relations, branding, advertising and trade show coordinating.